Welding jobs are expected to grow 6 percent by 2026, reflecting the need for welders, cutters, solderers and brazers in manufacturing and construction, notes the U.S. Bureau of Labor Statistics. This employment growth recognizes that welding is a significant part of the manufacturing process, particularly advanced manufacturing, as well as instrumental in rebuilding the country’s aging infrastructure – buildings, bridges and highways. Welding occupations also are instrumental in constructing new power generation facilities, and oil and gas pipelines.
Yet many manufacturers and specialty trade contractors are finding it exceedingly difficult to find skilled welders to fill current positions, let alone future work. It’s part of an escalating workforce crisis the manufacturing and construction industries have struggled with for decades as older skilled workers retire. Many young people aren’t interested in a career in the trades – or get talked out of it by well-meaning but misinformed teachers, counselors and parents.
With the U.S. economy continuing to grow, resulting in increased demand for goods and services, how do we recruit and train the next generation of welders?
“It’s a two-pronged approach,” explains Scott Lynch, CEO of the American Boiler Manufacturers Association (ABMA), Vienna VA. “One is working directly with schools to try to recruit people into the industry. But the other end of it is to work on the perception of our industry. We are not the old manufacturing (sector); we have innovative solutions and work with cutting-edge technologies to produce high-efficiency products. Welding is an exciting career no matter what part of the sector of the boiler industry you choose.”
He notes that many ABMA member companies have open welding jobs they can’t fill – partly because young people aren’t entering the trades, partly because of the skills gap for advanced manufacturing and partly because many boiler manufacturers are located in more rural areas. That location issue seems to be an even more pressing concern when filling engineering positions.
“Many of our companies are not in hubs for work – they’re not in Chicago, Philadelphia or LA,” Lynch says. “Companies that are in small towns and remote areas, they don’t have a large labor pool to pull from. Attracting somebody to an area three hours from a major city – when they are used to the perks of an urban area – is a challenge.”
With all that in mind, the Miami FL-based American Welding Society (AWS) is diligently working to change the perception many have about the welding industry and to promote welding careers as lucrative, exciting and stable. One extremely visible tool is the AWS Careers in Welding mobile exhibit, a 53-ft. trailer that is on the road 18 weeks a year, traveling to various events around the country.
“We take our mobile exhibit to state fairs, to farm shows, ag shows, air shows – any large event where families are in attendance,” explains Monica Pfarr, executive director of the AWS Foundation. “We don’t go to shows where we’re preaching to the choir, where we’re talking to individuals who are already involved in manufacturing or construction or welding. We’re trying to inform and educate the general public about career opportunities available in welding.”
She notes that roughly 28,000 people visit the trailer each year. There is no live welding on the trailer; instead, people use virtual reality welding simulators to try welding in a safe, fun, computer-generated way.
“For young people, they’re very excited about trying it out because it’s like a video game, something they’re familiar with,” Pfarr says. “It actually gives them a score at the end and says something like, ‘You performed 80 percent on your weld. Here are some things you could have done to score better. You could have kept the torch closer to the material or moved a little bit more slowly.’”
The trailer also includes other hands-on exhibits that introduce welding as a career opportunity and showcase other occupations available in the industry, such as engineers, inspectors, technicians, sales representatives and distributors.
Education, Training, Support
Once the interest is there, proper education and training are crucial to producing skilled welders to the boiler manufacturing industry, Lynch notes.
“Welding is an art, not a science,” he says. “There are basic requirements but welding itself is something that takes time and talent to learn. The challenge for our members is welders coming out of school have very basic welding knowledge and skills that are not transferable to our members. Boilers use high-pressure materials and parts, and they have to withstand significant high-pressure situations, which means they need a more durable weld than a plumbing system would need. Many of our member companies can’t fill welding jobs because applicants don’t have the right skill set.”
To help welders prepare for a career in the boiler industry and close the skills gap, Lynch says ABMA first needs to work with its members to determine the skill sets needed for each level of welding. The next step is to collaborate with community colleges near a group of member locations on developing a curriculum to teach welders the skills they need to succeed in a boiler manufacturing environment.
“We could bring in guest lecturers from our member companies to teach these more advanced skills,” Lynch explains. “But it’s important to make the welding students aware that if they are interested in going into an advanced manufacturing facility such as in the boiler industry, they need an additional level of experience.”
Lone Star College, with six campuses in the Houston area, has an extensive welding program, not surprising for an area dominated by the oil and gas industry. The college has 90 welding training stations across the six locations; the newer ones are three-phased so that students can learn three types of welding.
“We are updating one of our older labs right now with 45 brand new welding training stations,” notes Linda Head, Lone Star's senior associate vice chancellor of workforce and corporate partnerships. “We’ve added special brazing and welding inspections to the curriculum. We’ve integrated the AWS competencies so that when a student finishes one of our certificates or degrees, they can sit for the national test.”
Investing in the Future
Financial aid is critical for many welding students to continue their studies, especially for those students who are unemployed or with very low income, Head says.
“We have many students who are the working poor or are supporting families, and money is really important,” she explains. “They may have a job but not qualify for financial assistance. We have found scholarships are a fantastic way to be sure students can take care of their families without having to give up their education.”
Pfarr agrees: “AWS has done a lot of research and one of the big barriers for students is paying for their education. Obviously, scholarships help students with that. Once we’re able to get a student interested in pursuing welding, of course the next question they ask is, ‘How am I going to pay for it?’ If we can help them pay for their education, we eliminate that barrier and we have much more success in getting a student to actually pursue welding, complete the program and join our industry.”
ABMA has endowed an advanced welding scholarship through AWS and administered through Lone Star College to recognize achievement in specialty welding and raise the profile of the boiler industry as a destination for trade school graduates. The $30,000 scholarship would be awarded to a student that is enthusiastic about a welding career, interested in lifelong learning and working toward an advanced welding opportunity and potentially employable by a boiler company.
Lynch says the first scholarship winner will be announced this June.
Women Welders: The Next Great Wave?
Today, welding jobs are found in plumbing and HVAC (36 percent of total jobs), commercial and institutional building construction (6 percent), sheet metal work manufacturing (27 percent), fabricated structural metal manufacturing (27 percent) and temporary help services (1 percent), reports labor market analytics firm Emsi. Nearly 75 percent of people in welding occupations are between 25 and 54 years of age, and only 4.6 percent are women.
Chicago Women in Trades (CWIT), a group designed to improve women’s economic equity by increasing their participation in high-skill, blue-collar occupations, offers a 12-week welding program for women to enter either manufacturing or construction. The construction industry program is a pre-apprenticeship program that shows women what the different trades do, as well as talk about the physical abilities necessary to be competitive in labor-intensive jobs, explains Scarlet Burmeister, a full-time welding instructor at CWIT.
“We offer welding training programs that incorporate MIG, stick and TIG electrical arc welding training,” she says. “The program also includes shop math, measuring skills and blueprint reading – an accessible training program for women who haven’t done any shop or any fabrication work, where they can get the skills they need to start out in the industry.”
CWIT visits many local job fairs, especially at the high-school level. Burmeister notes it’s important to reach out to young people early and encourage interest in the trades so they concentrate on the right subjects in school, such as math.
“I like to talk to teenagers, especially the girls – many of them have never even considered this type of career,” Burmeister notes. “I say, ‘Hi, I am a welder. Maybe you would like to do this, too?’ For many young girls, it’s the first time they’ve been presented with that option.”
Pfarr says AWS is encouraging more women to consider a career in welding, focusing on job opportunities, higher pay and little college debt. In fact, so far this year, 16 percent of the scholarships AWS has awarded were to women.
Burmeister’s advice for women considering a career in the welding trades: be curious and do your research.
“Watch some videos of people doing the work, reach out to organizations such as Chicago Women in Trades and find out what those career paths look like, what type of people are doing them and what their experiences are,” she says. “The welding industry career tree is gigantic, and there are many different places it can take you.”
For more on ABMA Careers in Boiler Engineering and Fabrication, click here.
About the Author
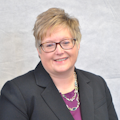
Kelly L. Faloon
Contributing Writer/Editor
Faloon spent 3 1/2 years at Supply House Times before joining the Plumbing & Mechanical staff in 2001. Previously, she spent nearly 10 years at CCH/Wolters Kluwer, a publishing firm specializing in business and tax law, where she wore many hats — proofreader, writer/editor for a daily tax publication, and Internal Revenue Code editor.
A native of Michigan’s northern Lower Peninsula, Faloon is a journalism graduate of Michigan State University. You can reach her at [email protected].