Pandemic Gives Boost to Remote Technologies on Jobsites
By KELLY FALOON, Special to HPAC Engineering
As you read this, two U.S. COVID-19 vaccines are now in the distribution stage, providing a light at the end of our very long pandemic tunnel.
Meanwhile, doctors also are getting better at treating the disease, another encouraging sign. And despite variants of the virus cropping up around the world and in the U.S. this winter, many health experts still say we could start getting “back to normal” by the fall of 2021.
But what will “normal” mean in 2021 for the construction industry?
For now, we still must deal with a highly contagious airborne infection. How do project managers ensure the safety of their crews while on a jobsite? How much of that work can be done remotely to optimize the time field crews spend on any given site?
Project coordination was the first process to incur changes because of the pandemic, notes Sean McGuire, director of innovative technologies at the Mechanical Contractors Association of America (MCAA).
“While much of the coordination work was already conducted via some online platform, internally there’s so much change because it's difficult to get all the right people in the same room,” he explains. “Usually, these internal meetings included the person doing the virtual design and construction (VDC) coordination and the fabrication, the project manager, the estimator and some leadership involved as well. They would come up with a game plan and execute it.”
With COVID-19 restrictions in place, much of this work is done virtually.
“With platforms such as Autodesk BIM 360, Revizto or Trimble Connect, you can embed a lot of the documentation and the data and some of the planning into the actual software itself, as opposed to keeping it on a standardized communication platform such as Microsoft Teams,” McGuire says.
Of course, while much of the planning can be conducted remotely, project managers and engineers still need to look at the physical site. McGuire notes some software platforms allow these team members to get a bird’s eye view of the situation on the ground.
With that in mind, a platform such as StructionSite (www.structionsite.com), Cupix (www.cupix.com) or OpenSpace (www.openspace.ai) allows users to perform a quick 3D scan of the construction site using 360-degree cameras.
“You shoot the video on a 360 camera as you walk a jobsite,” he explains. “It creates a lightweight 3D photogramatic model where you can see what the conditions are at the jobsite. The time it takes to shoot and process the video are a fraction of what it would take to use a laser-based 3D scanner. The file size is small enough to view in a web browser. You can navigate around, almost like you would with the street view on Google Maps, jumping from place to place and getting a 360-degree view of everything you need to. You can see what the progress is, or at least as of the last time they shot it.”
McGuire adds that this type of software also is a good tool for site documentation — where and when a particular piece of equipment or a section of piping was installed.
For more precise measurements, engineers and contractors can do a fully rendered 3D scan of the construction site using a phase-based scanner such as Trimble F7 (geospatial.trimble.com) or Faro Focus (www.faro.com/products/construction-bim). However, due to the amount of time it takes to capture the scan, process it and the size of file it produces, it is not feasible for weekly project updates.
“Phase-based scanners are great for field verification before and during a project," McGuire notes. "Before you install plumbing or mechanical work, you want very precise measurements of site conditions so that you can accurately prefabricate to 1/4-in. Small differences have a huge impact when fabrication no longer fits in the space as intended.”
Prefab still on the rise
Significantly, increasing the amount of fabrication for each project also helps with social distancing on a jobsite. There already had been a rise in prefabrication over the last few years, but since March 2020, the increase is significant, McGuire notes. Increased interest in the construction method reduces onsite involvement as much as possible as contractors, engineers, and project managers navigate building work during the pandemic.
“When you have a fabrication facility, it's a controlled environment,” he explains. “That means you can enforce COVID-19 protocols and create conditions that are spaced out. You're not relying on a general contractor or a construction manager — you can implement them directly. And off-site construction facilities allow you to run multiple shifts if you need to. Not only are you keeping your employees as safe as possible, but you're also doing your best to keep up with the schedule.”
Typically, workers in fabrication facilities work by themselves in a specific work zone. Tools, supplies, equipment and machinery are situated so workers are spaced out efficiently and have ready access to what they need to complete their tasks. And according to the construction schedule, the completed modules are transported to the jobsite and assembled.
“There are going to be limitations of how many people can work on jobsites, which slows down productivity,” McGuire notes. “By doing as much prefab as you can offsite, it helps you keep up with the schedule more easily. Most contractors with fabrication facilities have been pushing prefab more since last March. There's just no way around it. It's how they're protecting their employees and keeping up with schedules.”
Putting IT to the test
In north suburban Chicago, the Oracle Industries Innovation Lab (formerly the Oracle Construction and Engineering Innovation Lab) offers a simulated worksite for construction and engineering firms to experiment with different technologies to increase efficiencies and productivity in the built environment.
Phase 1 of the project opened in August 2018; we chronicled its progress 16 months ago here. Before the start of the pandemic, more than 1,000 people had visited the research facility to test how leading-edge solutions such as connected devices, autonomous vehicles, drones, augmented reality, visualization and artificial intelligence tools can positively impact the construction industry.
In November 2019, the technology firm announced it was expanding the Innovation Lab to include simulated environments for energy and digital communication solutions. But Phase 2 construction was hampered by the pandemic in spring 2020.
“Our project faced new complexities from the COVID-19 pandemic,” notes Dr. Burcin Kaplanoglu, executive director of innovation, Oracle Construction and Engineering, as he moderated a May 2020 webcast regarding technology, social distancing and remote management (http://bit.ly/2M0ThYS). “Our project team needed to explore new ways to work that would help keep jobsites safe and follow guidelines around social distancing.”
He explained that last spring the tech firm went to a few of its Innovation Lab partners to help: Reconstruct (www.reconstructinc.com), a remote visual monitoring solution for jobsites; Smartvid.io, which uses artificial intelligence to reduce risk and overall incidence rates on sites; and Triax Technologies (www.triaxtec.com), for workplace safety, risk and efficiency management.
“Soon after discussions started, we were able to deploy worksite monitoring, virtual progress reporting, and social distancing technologies to respond to the new and very different set of challenges,” Kaplanoglu says.
As MCAA’s McGuire notes, digital documentation of construction jobsites can help keep engineers and project managers off the site when necessary. Oracle partnered with Reconstruct to offer this solution at the Innovation Lab.
“This technology uses the visual data to enable remote monitoring, coordination and communication,” says Mani Golparvar-Fard, Reconstruct’s co-founder and chief technology officer, during the webcast. “It provides transparent process views to eliminate potential problems, enhanced quality control and safer operations.”
Reality-capture data consists of videos and images captured by drones, 360-degree camera or smartphones. “We take that data and create 3D virtual reality models that are measurable and provide you with a street-view experience for navigation,” explains Golparvar-Fard, who is also an associate professor of civil and environmental engineering at the University of Illinois.
Drawings and models are integrated with the virtual reality models and illustrate what is actually at the jobsite versus what should be there, he adds. Once construction schedule data is added, users can compare reality vs. design — they can see how much work has been done each day compared to the scope of work.
Another emerging technology on construction jobsites is artificial intelligence.
Josh Kanner, founder and chief executive officer of Smartvid.io, partnered with the Innovation Lab to help with social distancing metrics. “Our goal was to help automate the documentation of social distancing, as well as other safety activities, and help produce automatic COVID-19 mitigation plans as well as help reinforce the right kinds of behavior on-site,” Kanner explains.
Smartvid.io’s AI is named Vinnie. The technology “pulls in project data from photos and videos, which are analyzed by the Vinnie for 60 indicators of risk — from PPE on workers to slip, trip and fall hazards,” he says. “Risk factors are summarized in automatic reports and provide documentation of your COVID-19 compliance program.”
Vinnie also examines images and identifies risks. For social distancing, the AI program looks at workers within 6 ft of each other, groups of 10 or more workers in a given area, as well as the proper use of required PPE (gloves, safety goggles, masks).
“Safety observations from site workers help create alerts to easily track a company’s COVID-19 observations,” Kanner says. “Once you track and close out, you know those issues were dealt with. And you have an auditable trail of how risk behaviors were seen and handled.”
The program provides percent compliance ratios to help move toward a positive outcome and generates analytics that measure trends at the company level.
Keeping workers socially distanced on the jobsite is a critical component of Triax Technologies’ Proximity Trace, which pinpoints worker locations.
“Many of our clients came to us in this environment with specific needs, to track interactions as they’ve been defined as potentially harmful to their workers on different project sites,” notes Michael Fraser, vice president of business operations at Triax, during the webcast. “Our team was able to leverage the backbone of our technology to create a new product meeting clients’ needs for social distancing alerts as well as contact trace reporting.”
Each worker is given a sensor (TraceTag) affixed to a lanyard or hard hat. Workers are notified of a close proximity event (within a 6-ft. range) via an audible and visual alert. Alerts can be muted for three minutes if close contact is warranted for a certain task. Close proximity interactions/duration are recorded on the tag until it connects with a gateway, where data is transmitted to the cloud. Gateways also log attendance in real time.
If a worker does test positive for COVID-19, information gathered by the TraceTag pinpoints who that person had contact with, as well as the duration of those contacts (guidelines recommend 15 minutes or less).
As we continue to navigate through this pandemic, it is crucial that jobsite crews, project managers and engineers are given the right training and tools to keep themselves, and other workers, as safe as possible. Increasingly, remote technologies are now among the most essential tools that can keep employees off jobsite until it’s absolutely necessary.
##########
The author is a contributing writer to HPAC Engineering, Contractor, and Contracting Business magazines. The former editor of Plumbing & Mechanical magazine, Faloon has more than 20 years’ experience in the plumbing and heating industry and B2B publishing. A native of Michigan’s northern Lower Peninsula, she is a journalism graduate of Michigan State University.
About the Author
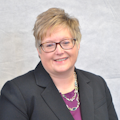
Kelly L. Faloon
Contributing Writer/Editor
Faloon spent 3 1/2 years at Supply House Times before joining the Plumbing & Mechanical staff in 2001. Previously, she spent nearly 10 years at CCH/Wolters Kluwer, a publishing firm specializing in business and tax law, where she wore many hats — proofreader, writer/editor for a daily tax publication, and Internal Revenue Code editor.
A native of Michigan’s northern Lower Peninsula, Faloon is a journalism graduate of Michigan State University. You can reach her at [email protected].